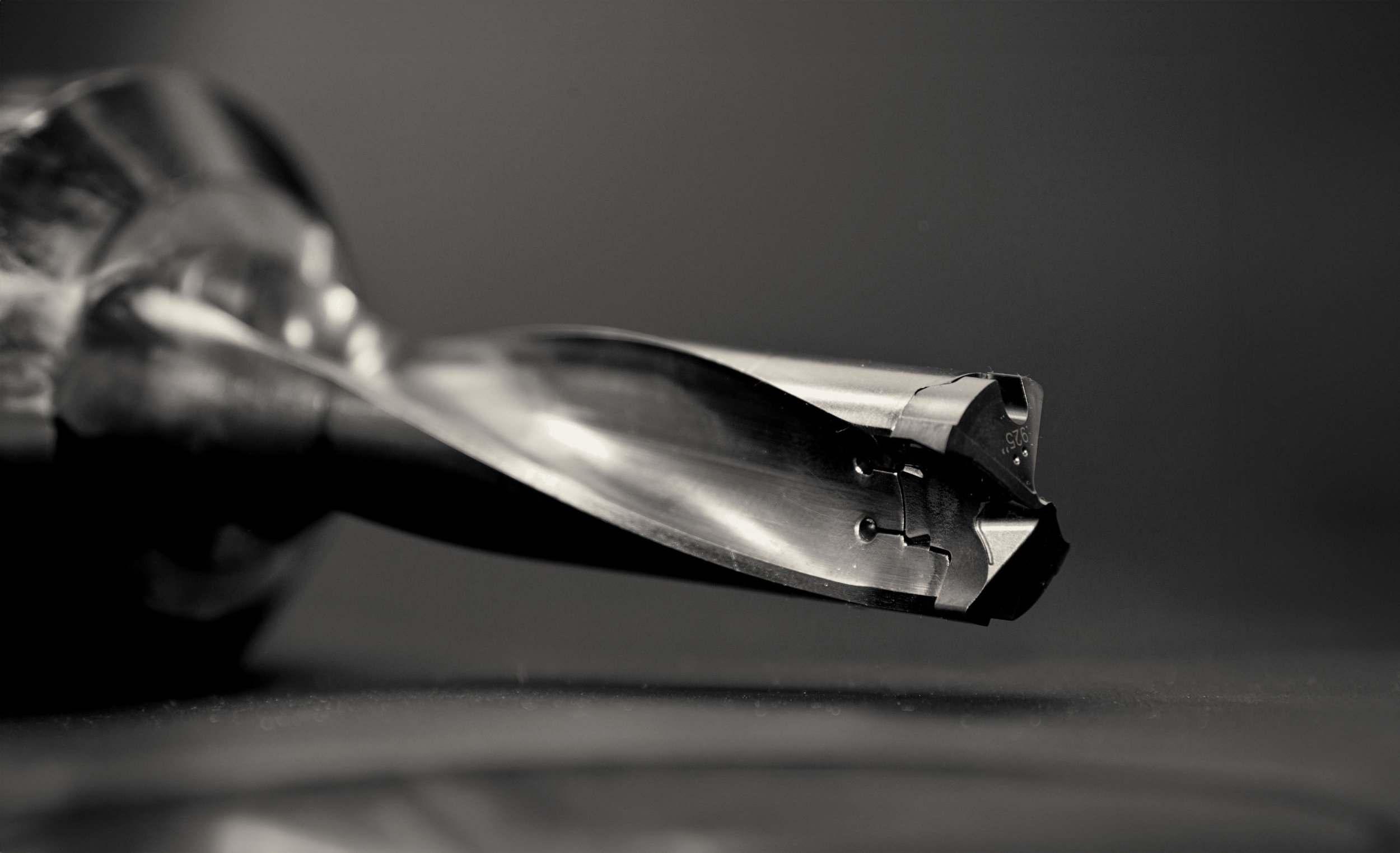
Advancing Maritime Engineering:
Precision, Innovation, and Collaboration
Leading-Edge Tooling and Prototyping
In the field of maritime engineering, transforming innovative concepts into tangible marvels requires unparalleled precision and cutting-edge technology. Our expertise in advanced tooling and prototyping stands at the industry's forefront, setting new standards in efficiency and quality.
By harnessing the power of advanced CAM milling, custom mold design, precision tools and jigs, and forward-thinking prototyping, we redefine the boundaries of maritime engineering. This introduction underlines our commitment to excellence, ensuring that from the initial concept to the final product, every project benefits from our deep technical knowledge and innovative approach, steering the future of maritime development with unmatched precision.
Advanced CAM Milling and Direct Molds
Custom Mold Design
Custom mold design is at the heart of our ability to meet a wide array of production requirements, making it possible to produce components that precisely fit the unique specifications of each project. Our approach involves a detailed analysis of the component's intended application, environmental exposure, and mechanical loadings to select the most suitable resin systems and reinforcements. This method allows for the production of GRP (Glass Reinforced Plastic) components that exhibit superior strength, durability, and weight characteristics. Our expertise in custom mold design enables us to offer solutions that are not only highly precise but also adaptable to the evolving needs of the maritime industry, ensuring that our clients receive products that meet their exact requirements.
Precision Tools and Jigs
The development and utilization of precision-engineered tools and jigs are crucial for maintaining the high standards of accuracy and consistency required in maritime engineering projects. Our tools and jigs are designed and manufactured with meticulous attention to detail, ensuring they meet the stringent specifications for time, cost, and quality. This includes the creation of custom jigs for composite lay-up processes, precision machining fixtures for metal parts, and specialized assembly tools that ensure components fit together perfectly every time. The use of these precision tools and jigs is indispensable for achieving the repeatability and quality control necessary for high-volume production runs, effectively minimizing variations and defects in the final products.
Prototyping and Pre-Series Development
Our approach to prototyping and pre-series development is characterized by a rigorous process that goes beyond the constraints of standard production workflows. By employing advanced prototyping techniques, including 3D printing, rapid casting, and CNC machining, we can quickly create and test prototypes that accurately represent the final product. This process allows for the identification and correction of potential issues in the design phase, significantly reducing development time and costs. Our capability to produce pre-series models provides valuable insights into the manufacturability, performance, and potential market acceptance of new designs. This strategic focus on early-stage development ensures that each model is thoroughly optimized and ready for efficient mass production, aligning with our commitment to excellence and innovation in maritime engineering.
Leveraging deep expertise in material science and advanced engineering techniques, our team excels in creating composite structures that redefine industry standards for performance and sustainability. Specializing in high-performance fibers and cutting-edge resin systems, we deliver lightweight, durable, and environmentally resilient solutions tailored to the demands of maritime engineering. This brief introduction underscores our commitment to innovation and precision, highlighting our focused approach in mastering the complex dynamics of composite construction to achieve superior results.
Expertise in Composite Construction
RTM (Resin Transfer Molding)
Resin Transfer Molding (RTM) is a sophisticated fabrication process designed for the production of high-quality composite parts. It involves injecting catalyzed resin under pressure into a closed mold where the fiber reinforcement has been placed. This method allows for complex shapes and detailed designs with superior surface finishes, thanks to the mold's ability to define the component's shape precisely. RTM is particularly effective for producing parts with consistent thickness, reduced weight, and increased strength, making it a preferred choice for automotive, aerospace, and marine industries seeking parts with intricate geometries and high-quality aesthetics.
Vacuum Bagging
Vacuum bagging is a composite manufacturing technique that uses a vacuum to apply uniform pressure across the laminate's surface during the curing process. By placing the lay-up inside a sealed bag and extracting the air, vacuum pressure compresses the composite materials against the mold. This process optimizes the fiber-to-resin ratio, removes trapped air, and ensures a compact, uniform laminate structure. The result is a product with increased mechanical properties, reduced voids, and improved bond strength, making it ideal for aerospace, marine, and sports equipment applications where performance and weight are critical.
Vacuum Infusion / Injection
Vacuum Infusion, also known as Resin Infusion or Vacuum Resin Transfer Molding, is a process where a dry fiber lay-up is placed inside a vacuum bag, and resin is then infused into the material using vacuum pressure. This method offers superior control over the resin-to-fiber ratio, resulting in high-quality laminates with excellent mechanical properties and low void content. Vacuum infusion is ideal for large-scale productions, such as wind turbine blades, boat hulls, and automotive panels, where consistency and structural integrity are paramount.
Hand or Spray Lay-Up of PE and VE Laminates
This technique involves the manual or spray application of polyester (PE) or vinyl ester (VE) resins onto a mold, combined with layers of fiber reinforcement. PE and VE resins are chosen for their robust mechanical properties, resistance to water and chemicals, and affordability. The hand or spray lay-up method is versatile and adaptable, suitable for a wide range of applications from boat hulls to industrial tanks. It allows for varying thicknesses and can accommodate complex shapes and sizes.
Gelcoat Application
Applying a gelcoat is the process of applying a high-quality finish to the surface of a mold. This protective layer, made from polyester or vinyl ester resin, is applied before the laminate, providing a smooth, durable surface that enhances the final product's aesthetic and protective properties. Gelcoats are available in various colors and can be tailored for enhanced UV resistance, blister resistance, and aesthetic qualities. They are widely used in marine, automotive, and architectural applications where a high-quality finish and surface protection are essential.
Hand Sanding and Polishing
Hand sanding and polishing are critical finishing steps that refine the surface quality of plugs, molds, and final composite parts. This meticulous process removes any imperfections, preparing the surface for painting, coating, or further processing. Skilled technicians perform sanding and polishing to achieve the desired finish, ranging from matte to high gloss. This attention to detail ensures that the final product meets the highest standards of quality and aesthetics, essential for high-end automotive finishes, marine vessels, and aerospace components.
Championing Sustainable Energy Initiatives
Our dedication to sustainability shines through in our leading-edge renewable energy projects, aiming to boost efficiency in wind and water power with innovative designs. These efforts underscore our commitment to not just advancing maritime technologies but also fostering a sustainable future.
Excellence in Project Management
Our meticulous project management ensures each venture reaches its milestones, drawing on extensive experience to manage the intricacies of new product development. Our approach is structured yet adaptable, enabling us to meet challenges head-on while focusing on our objectives.
The R&D Commitment
At R&D, we are devoted to advancing the frontiers of maritime design and manufacturing. Our comprehensive service offerings, commitment to innovation, and proficiency in advanced materials and methodologies affirm our leadership in shaping the maritime industry's future. We champion collaboration, innovation, and sustainability to not only build boats but to forge legacies.
Explore the future of maritime excellence with R&D. Join us in pioneering the next wave of maritime innovation. Visit us to learn more.
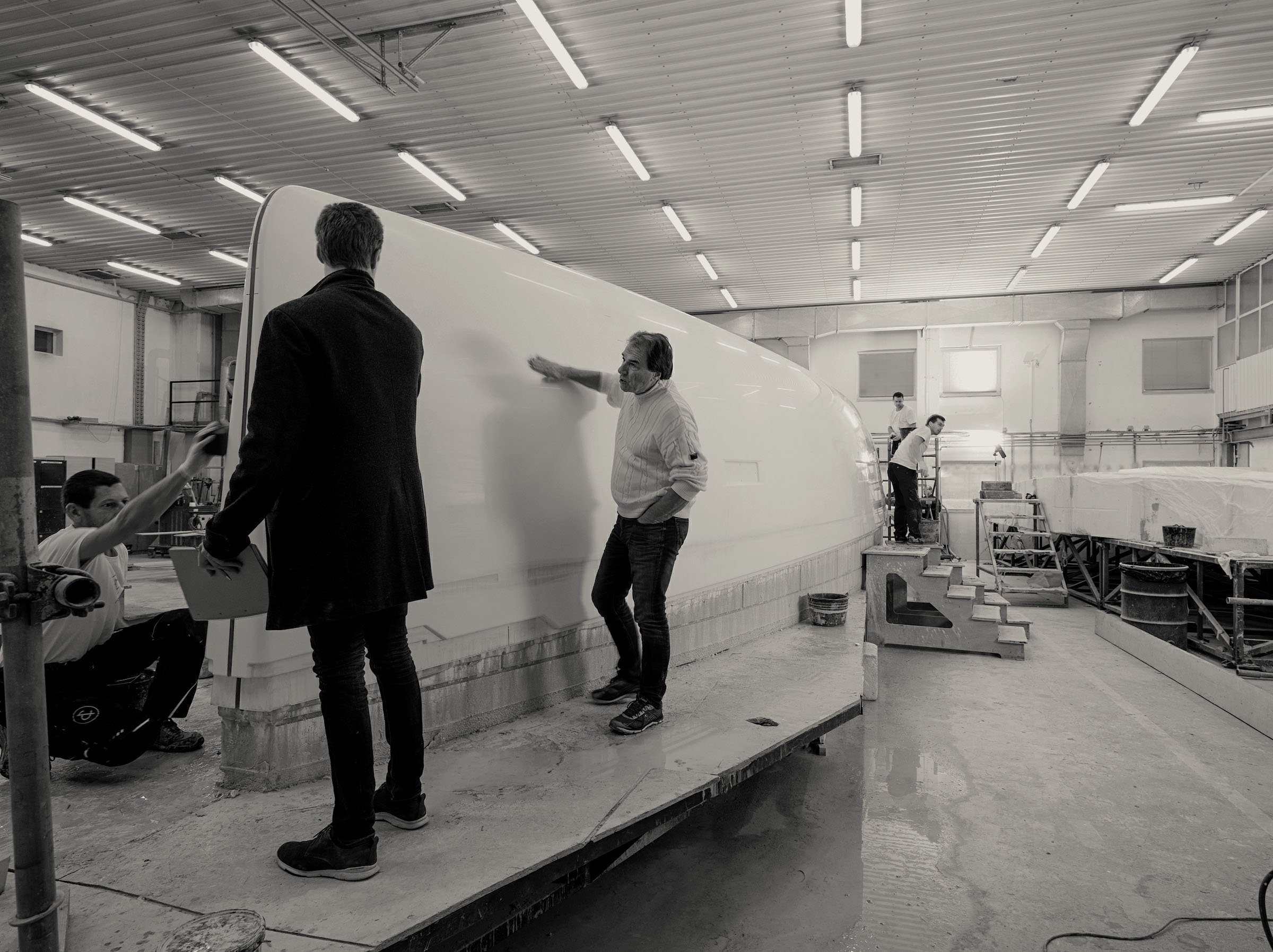